PVC Soft film plant
Soft PVC film used in : packaging industry, medical industry [urine bag], Rigid PVC film used in : blister [pharma industry], fills, packaging, decorative film, rim.
Special Feature : On Request
Customize machine as per customer requirement.
Rotating die for gauge deformation.
Urine bag extruding special mini film plant.
Rotating extruder for gauge deformation.
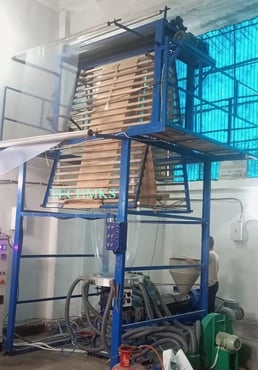
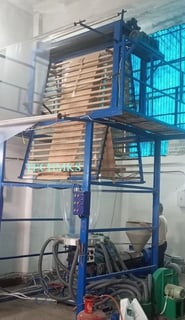
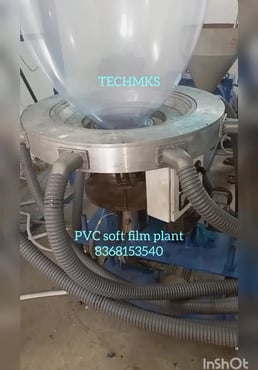
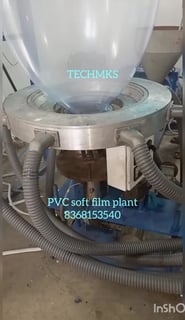
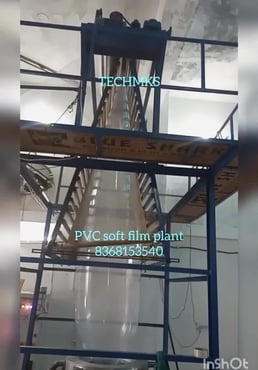
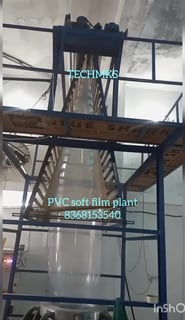
PVC Soft Rotating Die
Die Rotary Device for Film Blowing Machine is widely applied to producing the packing bags for foodstuff, clothing, rubbish bag and vest ones and etc.
Die Rotary Device is equipped with reducing motor to achieve low electricity consumption, no belts replacement, and high durability, noiseless during operation.
Die Rotary Device is specially designed for the extrusion die to blow the film very smoothly, evenly during rotating operation, it can be rotated to left and right within 360° angles, it can strengthen the intensity and greatly upgrade evenness of plastic film.
EXTRUSION BLOWN FILM SINGLE LAYER DIE HEAD ROTATOR FOR BLOWN FILM DIE HEAD
●TYPE OF DRIVING: GEARTYPE
●THERMO CONTROL:1~3 SETS
●APPLIED TO EACH MATERIAL
●Device Type :
1. With Temperature Control Box, Inverter, Reducing motor and Die Cart .
2. With reducing motor and die cartd, Without temperature control box and inverter.
3. With Temperature Control Box and Reducing motor, without Inverter, and Die Cart.
4. With Reducing motor, without Temperature Control Box, Inverter, and Die Cart.
LD HM Film Plant
Typically, Blown Film Plant Unit is carried out vertically upwards, however horizontal and downward extrusion processes are now becoming more common .
This procedure consists of four main steps:
• The polymer material starts in a pellet form, which are successively compacted and melted to form a continuous, viscous liquid . This molten plastic is then forced, or extruded , through an annular die.
• Air is injected through a hole in the center of the die , and the pressure causes the extruded melt to expand into a bubble. The air entering the bubble replaces air leaving it, so that even and constant pressure is maintained to ensure uniform thickness of the film.
• The bubble is pulled continually upwards from the die and a cooling ring blows air onto the film. The film can also be cooled from the inside using internal bubble cooling. This reduces the temperature inside the bubble, while maintaining the bubble diameter .
• After solidification t the frost line, the film moves into a set of nip rollers which collapse the bubble and flatten it into two flat film layers. The puller rolls pull the film onto windup rollers. The film passes through idler rolls during this process to ensure that there is uniform tension in the film. Between the nip rollers and the windup rollers, the film may pass through a treatment centre, depending on the application. During this stage, the film may be slit to form one or two films, or surface treated.
Cable and wire extrusion
TECHMKS is a reputed cable extruder machine manufacturer & supplier. It is known for its revolutionary product line carrying the best amalgamation of quality, cost, and delivery.
Each extrusion machine for building wires is not only fully guarded but also incorporated with IoT enabled hardware while following the industry 4.0 norms. The extrusion lines are available in single/dual/triple extrusion system with the ability to manage a wide range of products. The extrusion lines come with user-friendly interface and a self-diagnostic feature.
The Techmks extrusion lines provide high production speed, optimized processing, low energy consumption, settings customization, and work with versatile materials.
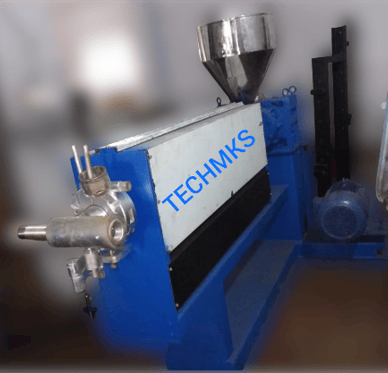
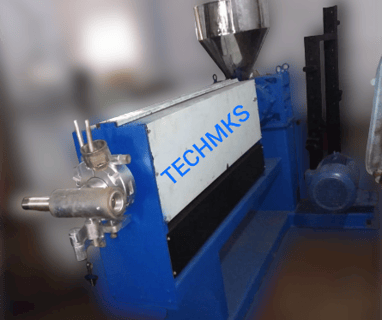